OKOndt UDS2-77 Ultrasonic Single Rail Flaw Detector

Have questions about buying this product?
The UDS2-77 ultrasonic single rail flaw detector is a handpush cart intended for the inspection of one rail line. The product is manufactured in nine modifications and can employ either Slide Search Unit or Roller Search Unit, and contain from 3 to 13 UT probes.
The flaw detector utilizes a unique scanning scheme that allows testing the entire rail section, except for foot flanges, by pulse echo, echo-shadow and echo-image techniques.
User-friendly operation
Both mechanics (the cart) and electronics (the software) of the UDS2-77 are ergonomically designed, have a user-friendly intuitive interface, as well as they are resistant to severe weather conditions that may occur during operation on a railroad.
Handcart design
- Weight of the cart is 16 kg only.
- Modular design of the cart consists of a support frame with adaptive rollers; electronic unit for control and visualization; multichannel unit (MUX); battery pack; couplant (water) tank; probe units; suspension mechanism of the probe units to place them into operation/transportation position; encoder.
- The position of the electronic unit for control and visualization can be adjusted along three axes
- The probe unit (slide or roller) is positioned cross-wise to the rail with the aid of a dedicated control device
- The probe unit can be centered using the adaptive roller
- The suspension mechanism of the probe unit ensures a stable coupling if the cart is tilted for up to 15°.
Probe units can be of two types
The UDS2-77 flaw detector employs contact probe units of conventional type with both standard and specialized probes.
The probe units are made from wear resistant plastic material, with hard-metal inserts on the working surface.
The slide probe units comprise the following probes:
Probe unit №1: | Probe unit №2: |
0° probe — 4 MHz | 4х58°х34° probe — 2.5 MHz |
70° probe — 2.5 MHz (Forward) | 70° probe — 2.5 MHz (Backward) |
4х58°х34° probe — 2.5 MHz | 2х45° probe — 2.5 MHz (Forward/Backward) |
1. One 4 MHz probe, 00 refracted angle is intended for inspection of the entire rail section by height in the web projection, for the presence of internal defects and laminations. This probe enables two testing techniques: pulse echo and echo-shadow.
2. Two 2.5 MHz probes, 700 refracted angle of (one of them emits along, and another — across the trolley movement) are intended for inspection of the central part of the rail head, for the presence of mature transverse defects.
3. Two 2.5 MHz probes, 450refracted angle (one of them emits along, and another — across the trolley movement) are intended for inspection of the entire rail section in the web projection, for the presence of internal defects, as well as for inspection of bolt holes for the presence of star-type defects.
4. Eight 2.5 MHz probes, 580 refracted angle that are turned by 34° in relation to the rail axis. The probes are placed in two cases, with 4 piezoelectric-crystal plates each. These probes enable pulse echo and echo-image techniques and are intended for flaw detection across the entire rail head.
Key features:
- Representation of test results in the form of A-scan, multi-A-scan, B-scan for all channels;
- Real-time display of test results in the form of B-scan
- Data recording and saving (operator’s name, line, direction, track number, left/right position, initial track coordinate, date, time, final track coordinate);
- Screenshot saving (PrintScreen);
- Saving of test results in the form of data array (B-scan) to the internal memory;
- Use of USB flash drive for transmitting test results to PC;
- Availability of measuring gates in A-scan & B-scan modes;
- Post-viewing of test result on the flaw detector with the possibility to measure conditional sizes of defects;
- Possibility to put the track markers (e.g. “Bridge”, “Crossing”, “Bolt hole”, etc.).
Suspension mechanism of Slide Search Unit
The suspension mechanism is responsible for positioning the slide probe unit in the rail head cross-section. It also ensures a steady acoustic coupling when the cart is turned by ±15°.
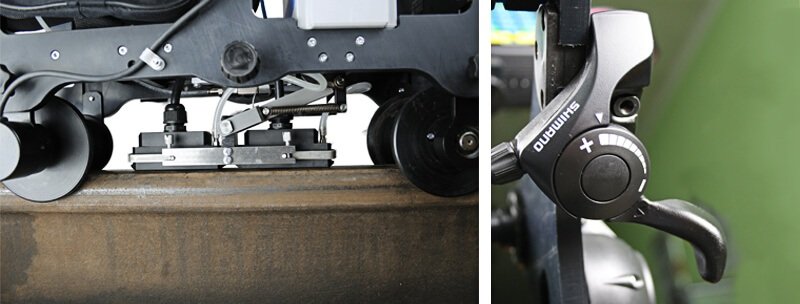
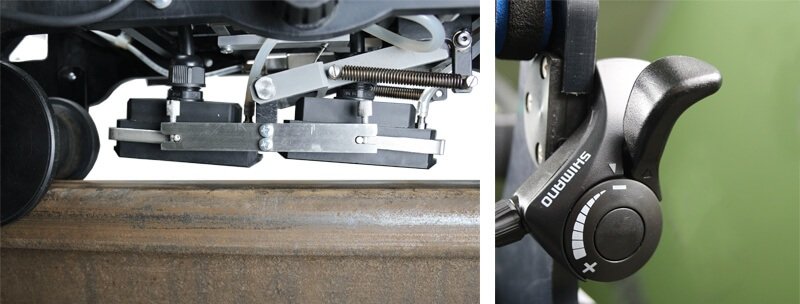
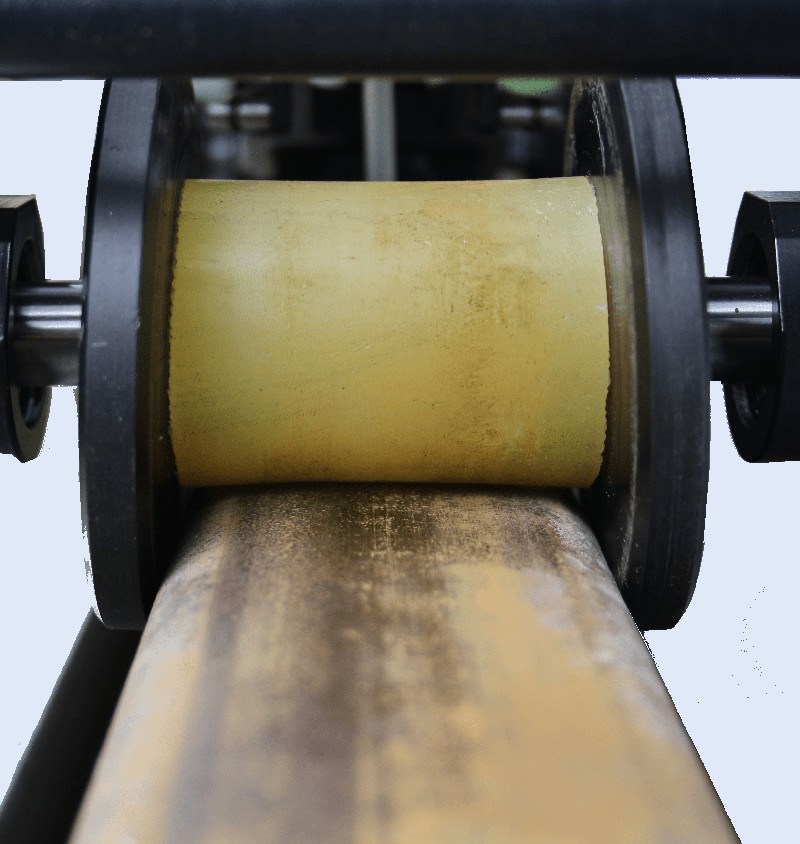
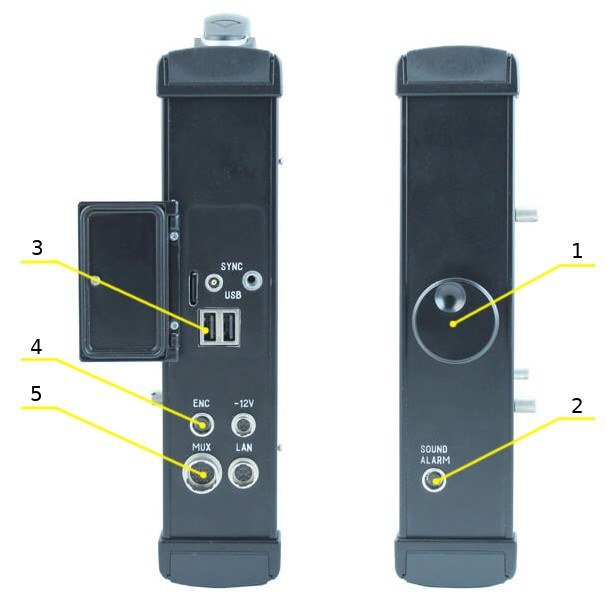
Electronic unit of UDS2-77
1 — Control Knob to change operation modes and parameter values in the software interface;
2 — Connector for headphones;
3 — Connector for USB-drive;
4 — Connector for Encoder;
5 — Connector for Multichannel (MUX).
Keypad
Keypad of UDS2-77 flaw detector consists of two navigation panels that are used for browsing through the menu items, modifying the parameter values, and calling for various operation modes with the aid of ‘hot’ keys.
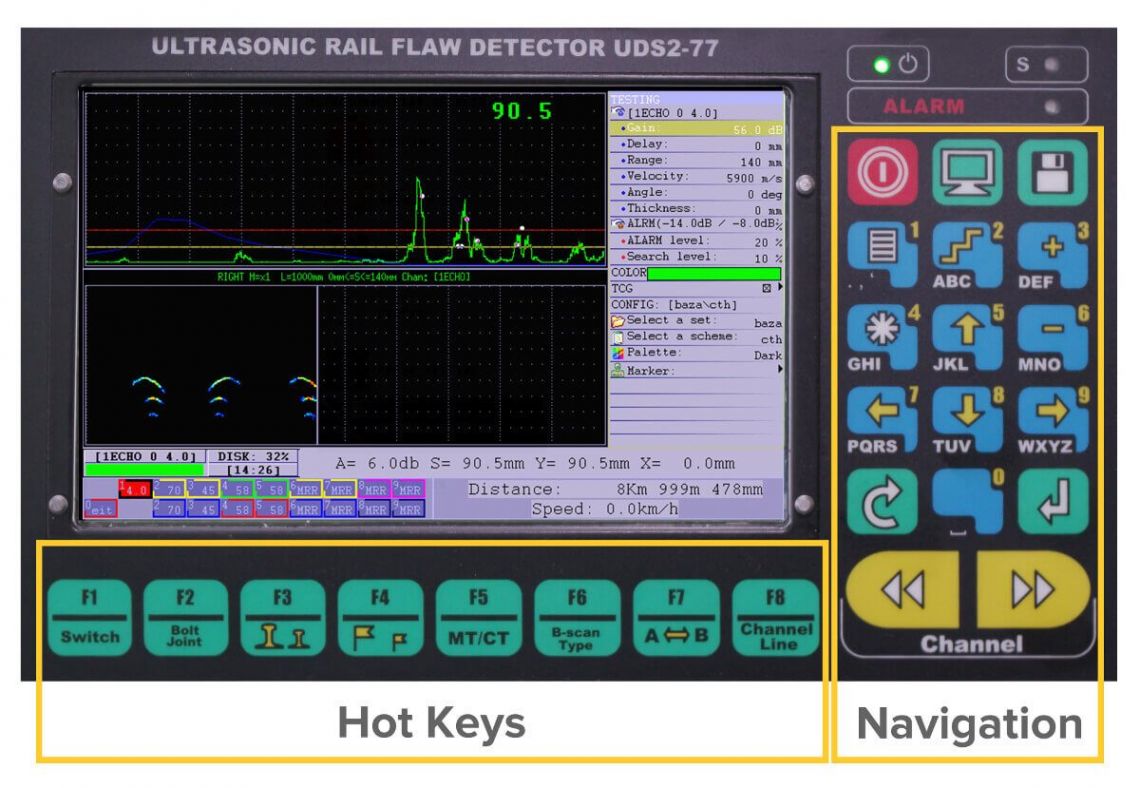
- UT techniques: pulse echo, (echo image) and echo shadow.
- Number of ultrasonic channels for 100% scanning: 13.
- Nominal test frequency: 1 to 6 MHz.
- Distance between probe pulse sendings: 1 mm at motion speed up to 5 km/h.
- Variation range of receiving path gain: 0 to 100 dB, with a step of 1 dB.
- Memory capacity for data storage: not less than 8 Gb.
- Weight of the flaw detector without battery and couplant: up to 16 kg.
- The flaw detector is powered by an independent power source (battery) with the rated voltage from 10.8 to 14.6 V and rated capacity of no less than 18 А·h.
- Time of operating mode setup: up to 15 sec.
- Time of continuous operation of the flaw detector with a fully-charged battery: no less than 8 hours.
- Protection rating: IP 64.
- The following alarms are generated during flaw detection: light – separate for every rail and common (via all test channels); sound – separate for every rail and common (for a group of channels); visual, on the screen – separate for every rail and every channel.
- GPS system is used to determine defect location coordinates on the track.
Software description | The UDS2-77 features a simple menu structure for setup and calibration, as well as setting of software functions/modes. The device is furnished with the Hot Keys panel to get an immediate access to main operation modes, such as display (А-scan/B-scan), correction of track coordinate, generation of test report, On/Off button for test result saving mode. |